어떻게 해야 표면 처리를 하고 나서도 선명하게 2차원 코드를 유지할 수 있을까요?
제조의 디지털 전환을 위해 초기 공정부터 ID 관리가 필요한 경우 2차원 코드(2D 코드)가 매우 중요한 역할을 하기 때문에, 인쇄한 2차원 코드 각인이 표면 처리 공정 후에도 사라지지 않아야 합니다. 하지만 레이저 마킹으로 인쇄한 2차원 코드는 표면 처리 공정을 하면 사라지기 때문에 추적성이 좋지 않다는 이야기를 많이 접합니다. 어떻게 해야 표면 처리를 하고 나서도 선명하게 2차원 코드를 유지할 수 있을까요?
대표적인 표면 처리 공정에는 카티온 전착 도장, 도금 도장, 열처리, 쇼트 블라스트가 있습니다. 이 중에서 카티온 전착 도장으로 표면 처리를 했을 때의 테스트 이미지입니다.
보이는 것처럼 표면 처리 후에 인쇄가 사라지기 때문에 2차원 코드를 읽을 수 없습니다.
표면 처리 공정 전 |
표면 처리 공정 후 |
 |
※ 카티온 전착 도장 |
기존 공정에서는 주조 후 표면 처리를 하면 개체 식별이 불가능 하기 때문에 주조 시에는 로트 단위로 관리한 후, 출하 전 표면 처리한 개체 위에 2차원 코드를 새긴 후 조립하는 방식이 일반적입니다. 그러나 표면 처리 전에는 로트 단위로만 이력을 추적할수 있기 때문에, 일관된 추적 관리가 어렵습니다.
일관된 추적 관리를 위해서는 어떻게 해야할까요?


파나소닉의 고출력 타입 화이버 레이저마커
마킹 방법과 출력을 잘 제어할 수 있다면
표면 처리 공정을 극복하고 2차원 코드 읽기가 가능합니다.
※사진은 테스트를 위해 깊게 새겨 실제 사용과는 다를 수 있습니다.
매우 깊게 새기기 때문에 표면 처리 공정 전에 인쇄해도 처리 후에 인쇄가 사라지지 않기 때문에 2차원 코드를 안정적으로 읽을 수 있습니다. 따라서 일관적으로 개체를 식별할 수 있고, 제조의 디지털화에 있어 추적 관리를 구축 시 매우 유용합니다.
일관적으로 추적 관리가 가능할 때, 어떤 이점이 있을까요? |

품질 데이터 연계&추적
불량 발생 시 제조 과정에서 원인 규명이 가능하고 병목 공정 개선에 기여합니다.

재료 로트 연계&정보 파악
불량 발생 시 원자재에 대한 원인 규명에 기여할 수 있습니다.
공정 누락 방지
각 공정에서 2차원 코드를 통해 중요한 공정이 누락되지 않았는지 확인할 수 있습니다.
표면 처리 공정을 넘어선 2차원 코드 인쇄는 단순히 레이저 발진기 출력이 높다고 실현되지 않습니다. 파나소닉 인더스트리는 반복적인 실험을 통해 축적한 노하우로 고객의 문제 해결을 제안합니다. 관심이 있으시다면 아래의 버튼을 통해 상담 요청 주시기 바랍니다.
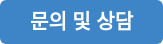
레이저 마킹기